Silver Bullet Big 10
Silver Bullet – Big 10
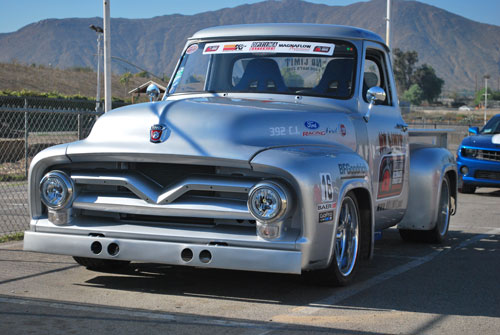
What do you do when a successful road racer like Boris Said and a chassis engineer, (enter Rob Macgregor) get together to build a truck? That’s the story behind No Limit Engineering’s new BIG 10 Chassis, available for Ford F-1, F-100 through 1956, and Chevy ½ ton 1947 through 1959 pick-ups.
You say that you don’t know who Boris Said is? Well he’s better known as the “Road Course Ringer” to his NASCAR Sprint Cup competitors, with SCCA wins at the 24 hours of Daytona, the 12 hours of Sebring, and many NASCAR Truck series wins. He really knows what it takes to drive anything hard and fast. The same goes for Rob Macgregor. A newbie by no means, Rob has been “El Jefe” at No Limit Engineering for over 25 years designing, building, and torturing classic pick-ups each and every day.
You may not be able to identify Rob from a police lineup, but you’ve seen his work. Responsible for contributing to multiple F-100 National winners, countless magazine cover vehicles, and the creator behind Goodguys 2005 “Truck of the Year” dubbed “The Princess” Rob has held his own.
How did these two meet? From a referral from a suspension manufacturer that is mutual friends with both Boris and Rob. When Boris decided to build a 1956 Ford F-100 for himself, they sat down to hammer out the details of what would be required to make a truck really work, something that is fast enough to take on a sports car, strong enough to dish out a whooping, and comfortable highway comfort during long hauls cruises to the track, or a coffee shop run down by the coast.
With a clean sheet of paper, the guys set out to cure some of the common problems owners face when attempting to modernize a classic pickup. Trucks are known for ill handing, poor brake performance, and horrible steering woes. To their credit, classic trucks were designed as “tractors with doors” and never meant to out-corner a sports car.
Right away Rob and Boris both agreed that most after-market chassis “flex” while cornering. The typical 2X4 inch box tube chassis’s weight transfer creates an enormous amount of load which is too much for the frame rails to handle. Even more, the weight balance of the truck has always been a problem, so they addressed that right off the bat. In doing so, they didn’t want to add more weight to the chassis creating the need for an expensive power plant to compensate for adding weight.
The answer is what you see in front of you. The first thing you see when looking at the BIG 10 is the size of everything. Engineered in sections, the weight is now properly placed towards the center of the truck, where it’s needed most. In doing so, this balances the weight of the vehicle, disbursing load over both axles rather than having a “light” rear end. The name itself comes from the size of the center section of the chassis; a full ten inch tall frame rail is designed from channel, and not box tubing. To cure the “flex” a massive “X-member” is engineered into the center section.
Out back, the theme of rerouting weight to the center of the chassis is easy to spot how the boys intended it to do. The axle travels through the frame rather than under the frame, again, transferring weight back to where it is most needed. The same goes for the front section. Utilizing the Wide Ride IFS success from No Limit’s “Pro Tech” chassis, improvements were made in weight transfer during heavy “G” loads while pushing the truck through the paces. All of this has been achieved by maintaining the stock wheel base requirements, and engine / transmission mount locations, ensuring that the trucks’ sheet metal and factory items do not need modifications.
Now I know what you’re thinking; yes it’s big, yes it’s strong, so does it fit under my truck, and how heavy is it? Surprise! Yes, it has been engineered to fit under both Ford and Chevy applications without modifications, and will sit lower than any stock chassis. Further, the “channel” design of the frame doesn’t add any more weight than a stock chassis. Even better, the components that are required to build a chassis are computer documented, and manufactured for the home hobbyist to install using hand tools and a drill motor. This is a zero fab chassis!
The brake lines, cab mounts, fuel tank mounts, battery box, and so on have been engineered, fabricated, holes drilled and tapped ready for you to bolt together! No Limit’s philosophy is that if you can’t put this chassis, or a classic truck together with nothing more than a 300 piece tool set from the same place where your wife buys you flannel shirts, then we re-engineer it.
“Sure it’s a race car but I want to drive it on the street, on long trips with my wife carrying a couple of lawn chairs,” you might be thinking. We do too! Driving trucks is fun, and the BIG 10’s rear “Rocker” style shock linkage, and “trailing arm” set-up eliminates “road –hop” by design transferring the weight forward. Responsive steering via the rack and pinion set up feels like your everyday driver, smooth and positive, not all over the place chaos like that “old straight axle”, or “clip-job” done thirty years ago. It’s your choice to run either “Coil-Over” shocks or “Shockwave” adjustable air springs for additional cost.
Take a look at the pictures, and see it for yourself.
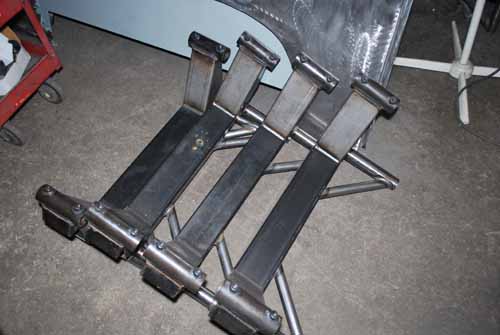
Here‘s a look at the meat and potatoes of the front independent wishbone suspension. The wide ride front cross-member is fabricated first before dropping it into the frame jig.
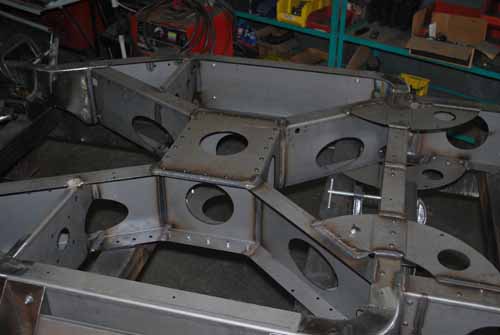
If the meat and potatoes are the front cross-member then the “center-section” is the heart. The “X” member transfers load while cornering, and makes the frame rigid.
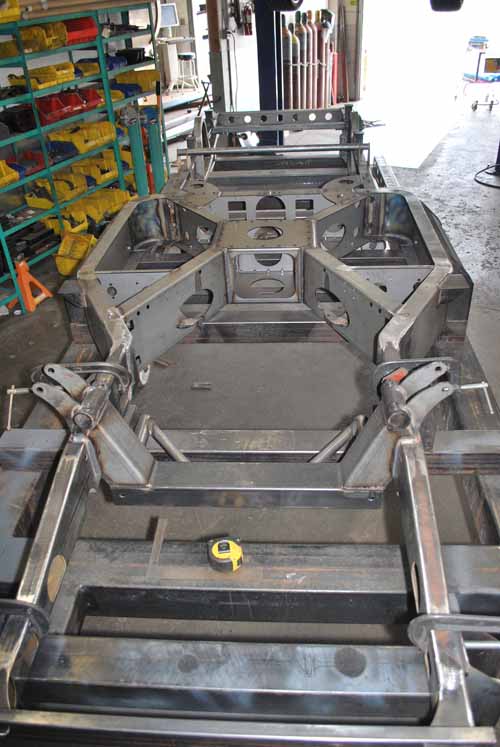
Each chassis is CNC laser cut and welded by hand one at a time in the Big 10 Chassis jig. Look how the wide stance of the Big 10 appears massive, but the use of channel material rather than “box” material saves on weight, in turn dissipating flex through the chassis during heavy “G” load situations.
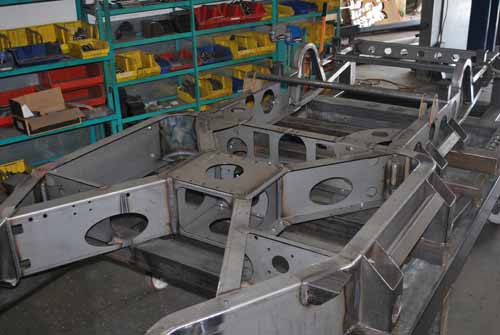
Rob thought of everything. Here you can see where the provisions for the brake system, exhaust system and transmission mounting have been carefully thought out and implemented for each chassis.
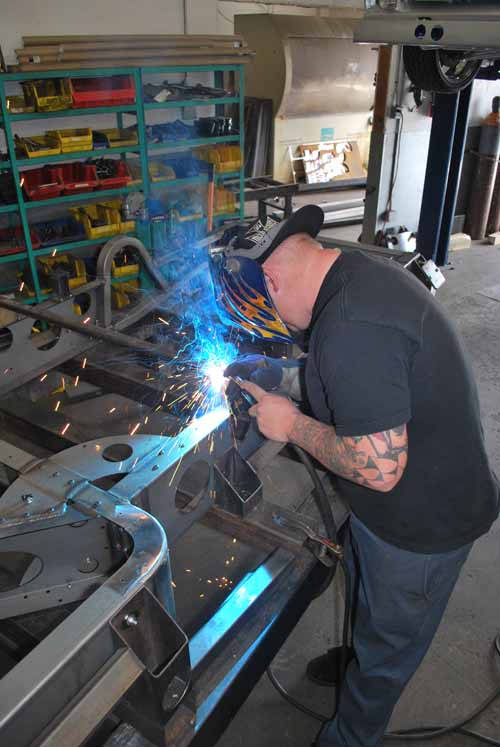
The pieces are set into the BIG 10’s jig and are hand welded. Here, Joe lays down some “Sexy weld beads” on another BIG 10 Chassis.
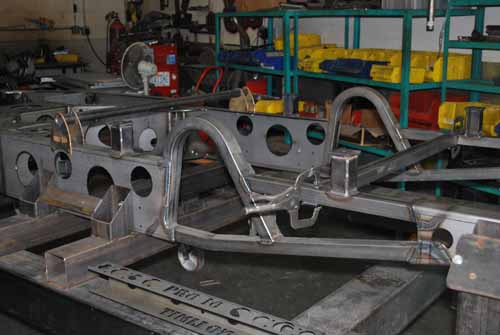
The rear section of the BIG 10 was designed to transfer the weight back towards the front of the truck. How did they do it? First by maintaining a connection of the frame-rails allowing the rear axle to “travel” in the frame and not under it, “G” load is re-routed back towards the front by keeping the rear of the trucks frame “rigid”. Also, the trailing arms change the “instant center” of weight balance forward. The results, this truck chassis hooks up and holds corners like that punk Camaro wishes it could!
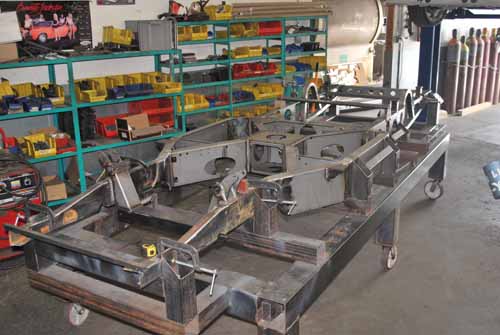
Here’s a fully welded frame in the raw ready to be sent out to its new home. Since they are a “zero fab” chassis, they can be sent out to powder-coat as an upgrade and shipped to your door via truck freight.
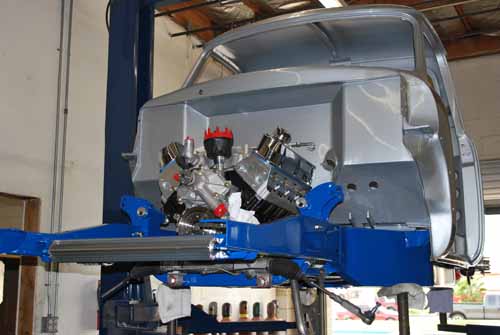
Back from the powder-coater, the cab and the engine “bolt-on” with ease in the first hour or so.
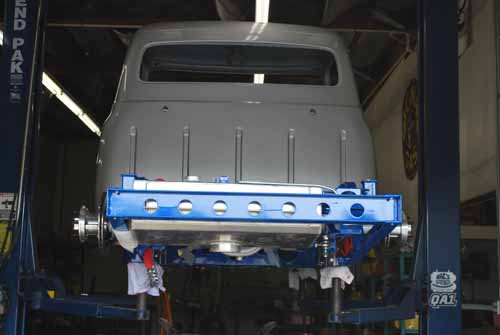
Here’s a look at the rear of the truck. The No Limit fuel tank and “drop-out” battery box fits nicely behind the rear axle providing weight balance to the rear of the truck.
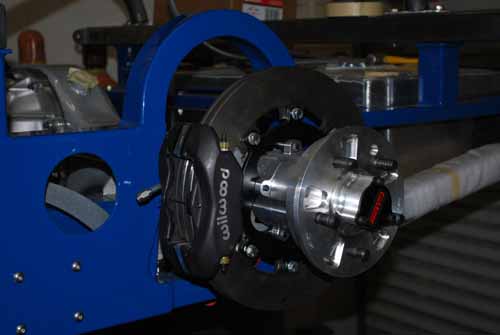
This application called for a Wilwood rear disc and a “floating” 9” rear axle. Note how the axle travels through the frame. Don’t worry, it won’t drag on anything. The frame rails hug the axle housing just enough to give it enough clearance to drive with but doesn’t hang down to get things stuck on it.
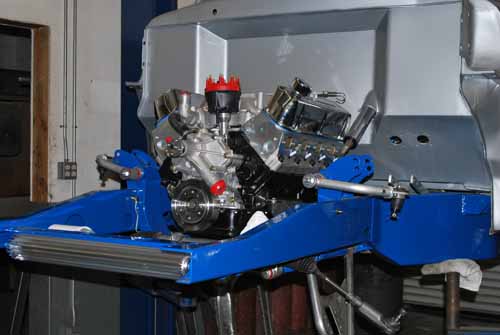
Take a look at how clean that 392 C.I. Ford Racing small block looks in that BIG 10 Chassis. Proper header clearance has been addressed, and even a partnership with Gibson Performance Exhaust has been created to have a ready-made exhaust system shipped to your door along with your new chassis. Once again, these guys thought of everything.
![]() |
![]() |
Years of R&D went into these spindles engineered at No Limit Engineering. Correct steer geometry has been achieved as the result, benefiting you the driver. Correct Ackerman and a better turn radius make up just some of the features of using these spindles.
![]() |
![]() |
An assembled look at the front suspension allows you to see the simplicity of the optional “shockwave” air spring and the mounting point of the anti-sway bar. Don’t forget to peep your eyes on those brakes as well.
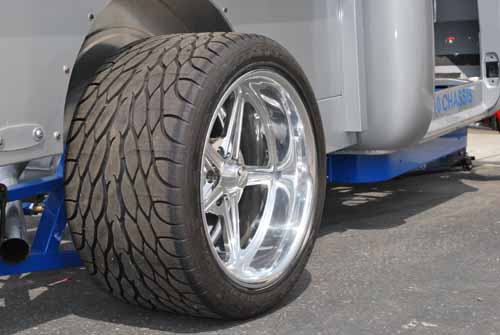
Hungry for some meat? Tire meat that is! This chassis will serve you up some and leave room for seconds. The 18”X 11” intro wheels, wrapped in 345X 40X 18 BF Goodrich tires, will fill your wheel wells up just fine. If you’re not that hungry, let us take your order on what size is right to your liking.
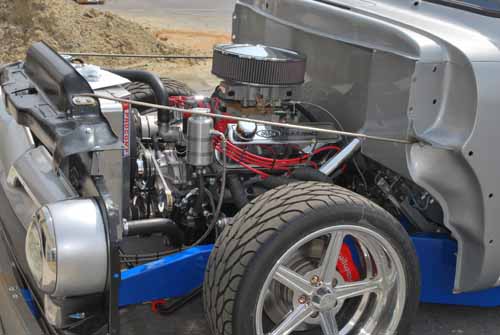
With the fenders and hood off, you can see how simple and easy everything fits, and works with this chassis.
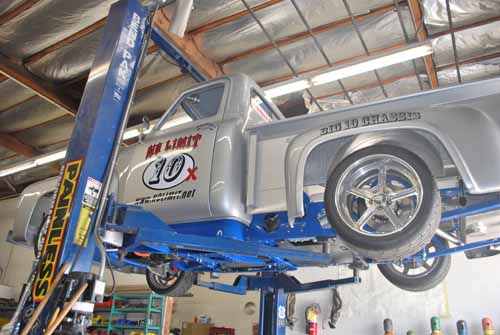
Up on the lift, you can tell just how tailor-made this chassis really is. Everything has its place, and it’s placed just right.
![]() |
![]() |
![]() |
Bam! If that doesn’t make you excited then call the doctor, you’re not living right my friend. The BIG 10 chassis really is a purpose built chassis for classic trucks. Willing to “talk the talk” and “walk the walk”, Rob couldn’t resist the urge to build one for himself, and can be seen auto-crossing it at the Goodguys Street Challenge in a city near you. Stop by and say hi, and be sure to ask to go for a ride.